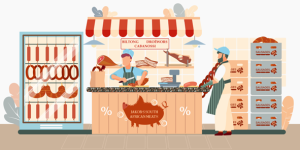
It was close to the end of the day, and Jakob was just starting to think about closing up his shop when the bell on the door rang and Pieter walked in.
“Pieter!” Jakob’s face lit up with a smile. “How are you, man?”
“I’m well, thanks,” Pieter replied. “I was passing by, and I realised it’d been too long since I had some of that biltong you make.”
Jakob could remember how Pieter liked his biltong, and he grabbed a stick and began slicing it for him. “You’re still with that consulting business, right?” he asked as he worked.
“That’s right,” Pieter replied. “It’s going well – I’m actually on my way back from a client site now. Why, did you want some advice?”
“Uh… maybe.” Jakob looked embarrassed. “Could you spare a few minutes while I close up?”
“Sure.” As Jakob went around the store, locking the doors and turning off the lights, Pieter leaned up against the counter. “So, what’s on your mind?”
“It’s the drying rooms,” Jakob said as he came back to where Pieter was waiting.
Pieter frowned. “You’re going to have to explain that, sorry.”
“Biltong has to be dried, right? And so does cabanossi, and droëwors, and all the other small goods I sell. There are three rooms we use to dry them, and we call them… drying rooms. Stop me if I’m going too fast.”
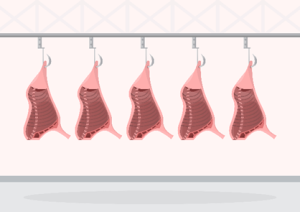
Pieter shook his head in exasperation. “I forgot how sarcastic you could be when customers aren’t around! OK, what’s the problem with these drying rooms of yours?”
“They always seem to be working on the wrong thing, or not working at all,” Jakob explained. “Look, I get some customers walking into this store, like you just did, but most of my business is filling orders to supply other stores. Those drying rooms are the bottleneck in my business because everything has to go through them, and there are only 24 hours in a day. We just can’t seem to get them operating as efficiently as I’d like.”
Pieter nodded. “OK, talk me through this. What do you do, and how does it go wrong?”
“At the start of the day, I look at all the orders we need to process and make sure it is up-to-date,” Jakob began. “I put them in a sequence so that they all go through the drying rooms by the date we need to ship them and give that list to the supervisors.”
“This all sounds good so far,” Pieter said. “What happens next?”
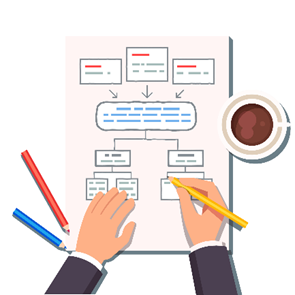
“The supervisors check we have the meat and other stores needed to fill those orders, then everyone gets to work. And that’s when the problems start…” Jakob sighed. “I try to keep the drying room list current, but somehow it never works as it should. The guys setting up the cutting and curing want to be as efficient as possible, so they grab all the stuff for the upcoming orders that can be done together. Which is good, right? But that means the orders start getting processed out of the sequence I had set up, so the stuff that gets to the drying rooms isn’t always what I had expected would make it in there that day.
And we can’t just open the drying rooms and change what’s in them when the orders reach the drying rooms, because that destroys the temperature and humidity balance for the stuff that’s being processed. Even though the drying rooms are operating constantly, I still end up having to tell customers that their order has been delayed. That’s not a good conversation to have with someone who’s expecting 250kg of biltong to arrive tomorrow afternoon, you know?”
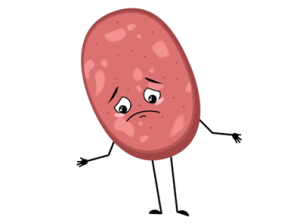
“OK, so you need to keep that sequence intact,” Pieter said thoughtfully. “The obvious thing to do is to just keep all the meat and spices and so on stored away, and people can only get what they need for the job they’re working on. Have you tried that?”
Jakob nodded. “Yep, and in some ways that was even worse. Doing that meant there were delays between jobs getting processed – it takes time to move 300kg of beef, and set up the curing trays, and so on. That meant orders were being started too late, and then wouldn’t reach the drying rooms in time.”
Pieter nodded. “Were you getting all the orders done?”
Jakob shook his head. “That was the other problem. We are getting gaps in the sequence at the drying rooms, and we can’t afford to stop and wait for the missing orders”
Jakob sighed heavily. “Honestly, I don’t know what to do. It seems like we’re stuck not getting things done in time, either because the sequence got messed up or because we were running incomplete loads.” He looked up at his friend hopefully. “Got any ideas?”
Pieter looked up at the ceiling while he thought. “Well,” he said eventually, “One thing we often tell clients is to time the access to jobs and the material that those jobs will use so that they line up. Synchronise it if that makes sense.
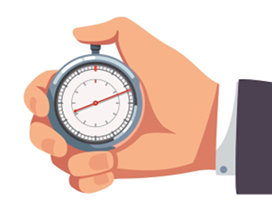
When one job gets finished, which in your case means coming out of the drying room, the next job gets released along with the material necessary to complete it. The advantage is that people can’t really get the jobs out of sequence, and you are ensuring that the right jobs reach the drying room – your constraint – to complete the day’s orders on time.
To make it work, you have to be looking into the future a bit and planning out what needs to be completed ahead of time… but you were doing that anyway, right? I mean, it takes time to dry the biltong and so on, so you had to be working a bit ahead anyway.”
Jakob nodded excitedly. “Yeah, we were. OK, let me think for a moment… so, for each drying room, I need to work out how many hours ahead its scheduled orders must be released, so that all those orders have finished cutting and curing prior to the time I want to close the drying room door. Man, I think that could work! Why didn’t I think of that?”
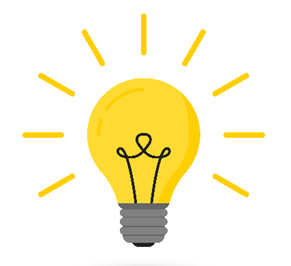
Pieter shrugged. “You’re probably focused on the day-to-day stuff – getting the goods out the door, getting supplies, paying wages, and so on. I’ve seen this problem before. It’s common whenever a large investment is made, as you did with the drying rooms. The investment leaves people very sensitive to maximising the return, and so like your rooms you care that they are full. Correctly, I might add, because if you don’t manage to do that the business will collapse. And when you’re up to your arse in alligators, it’s not easy to take a step back and look at things with a clear head.”
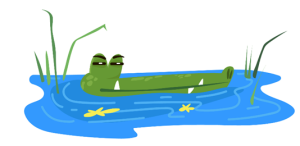
“Ain’t that the truth!” Jakob laughed. “Thanks, Pieter, I’m going to give that a try.”
“Do that,” Pieter nodded. “I’ll come back next week, and you can tell me how you got on.”
It was actually more like two weeks by the time Pieter got back to Jakob’s store, but when he did, he saw his friend grinning at him from behind the counter.
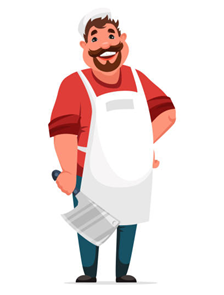
“Afternoon, Jake. You look like you’re in a good mood.”
“I am! You were right with what you said, things are going much better now.”
“I’m glad to hear it!” Pieter said. “So, you did end up synchronising the release of jobs and materials, then?”
Jakob nodded. “Yes. And it worked! Oh, there was a bit of trial and error to get the chunk size right – you know, how big each batch of jobs and its materials should be. When I planned out what to release today, later this week and next week, I found that the drying rooms would be full about half the time. It was tempting to add in next week’s customer orders and run them too. We’ve done that plenty of times before and it helped us stay in front. Fortunately, though, I realised that it would be better to fill the gaps with new sales. Let me tell you, that was amazing!
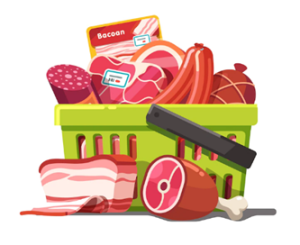
It used to be so common for customers who are passing through to stop in, only to find we have run out of their favourite biltong and then leave empty-handed. So, we choose to fill the gaps with small batches of some fast-turning items, so now we always have some stock on-hand. Orders are getting done on time and in sequence now, and the drying rooms are always full. Our output has actually increased a little bit too, just from getting the sequencing right. I’m amazed how much difference it’s made!”
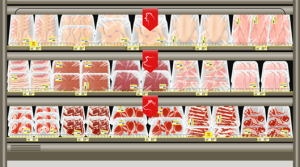
Pieter smiled at him. “Yeah, we hear that from clients pretty often. Small things can make a big difference, you know?”
“Well, I believe it!” Jakob laughed, then looked at Pieter speculatively. “Actually, while you’re here, can I get your opinion on something else? Now that the drying rooms are operating properly, there’s this other little expansion idea I’ve been thinking about…”
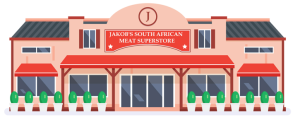