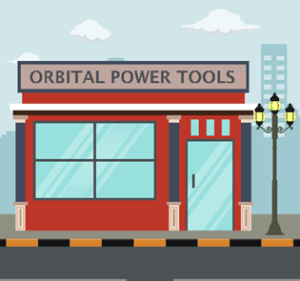
Julian stood up when a tall woman entered the room. Before he had a chance to speak, she walked up to him and shook his hand, smiling.
“Are you Julian? Tabitha Reyes, but call me Tabby – everyone does! You’re here to interview me, right?”
Julian blinked in surprise, but returned the handshake and managed a smile of his own.
“Yes, that’s right. I’m from ‘Big in Business’ magazine. Everyone’s talking about the difference you’ve made here at Orbital Power Tools, and our readers would love to hear the story as you tell it.”
Tabby nodded. “Right, that’s what the email said. I’m in a bit of a rush this morning, I’m afraid, so let’s get started. Take a seat,” she said and gestured to a couch and a couple of armchairs in one corner of the office.
While she was sitting down Julian took a glance at his notes, so he was ready when Tabby turned to him enquiringly.
“OK, so, first question: what is this revolutionary thing you’ve done here?”
Tabby laughed. “That’s your first question? You don’t start small… but OK, I’ll try to answer that.” She thought for a moment, then leaned back in her chair.
“I call my idea a ‘Common Parts Schedule.’ It’s basically a way of making sure that jobs get finished on time and overheads are kept low, even when there are a lot of jobs needing the same parts. It also helps us to keep lead times stable.”
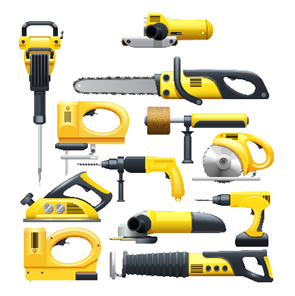
“Right, right…” Julian nodded. “Uh, could you maybe give us a bit of background on the situation? Like, what is it that made this necessary?”
“Sure thing. Here at Orbital Power Tools – OPT, as the cool kids call it – we make power tools. Stop me if I’m going too fast for you,” Tabby grinned. “We make quite a variety of them, for various purposes, but most of them need… these.” Tabby took a small metal object from her pocket and tossed it to Julian.
Julian caught it and examined it curiously. “It looks like a shaft bearing of some sort. It’s got ball-bearing raceways, and it’s maybe… 12mm in diameter. What is it for?”
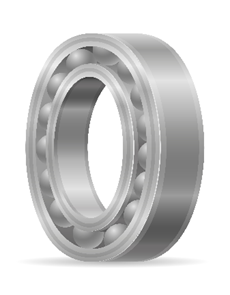
“You’ve got a good eye, it is 12mm. It’s a self-aligning ball bearing that reduces the rotational friction in our power tools. Anyway, most of our products have several of them. We get in the balls and so on and these bearings ourselves. Before I introduced the ‘common parts schedule’ we were making thousands of these bearings, and storing them for use later, but somehow, we kept finding that we had run out of the right bearing and urgent jobs had to wait for more to be produced. It was ridiculous!”
Julian frowned. “How did that happen? I mean, if you made plenty then why weren’t they available?” It didn’t make any sense!
“Fair question,” Tabby nodded. “To answer it… well, you know we run a constraint schedule here, right?”
“Yes,” Julian replied confidently. He’d done some research before coming here. “You’ve nominated a constraint, the armature assembly, and got everything working to support it, and so on. Standard Theory of Constraints stuff.”
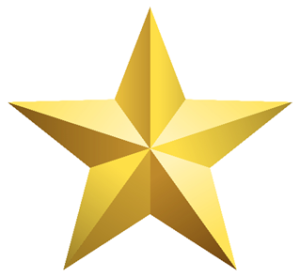
Tabby beamed at him. “That’s right! Gold star for homework, Julian! Anyway, almost all our products require motors with various shaft, rotor, and stator sizes. And, our people, when assembling the motors got into the habit of just grabbing bearings from wherever was nearest.”
“Ah…” Julian thought he was starting to understand. “So… some jobs that had gone through the armature assembly couldn’t be finished, because they were missing these bearings.”
“Exactly. And because of that, we got a whole lot of problems. Our constraint is the motor armature production, and that runs just fine. For some of our jobs we hold prebuilt armatures, but most we build from scratch. The issue was our completion schedule kept falling apart. We couldn’t predict which order jobs would get completed; we couldn’t predict when they would be completed. Further, the place was full of half-completed motors which were shoved to one side waiting for the right bearings, and those bearings were in hot demand!” Tabitha sighed and shook her head. “It was just a mess, Julian.”
“Hmm.” Julian thought for a moment. “The obvious thing to do is to just reserve all parts for the job they’re assigned to – do that for every job, and you’re sure everything has the parts it needs. I’m guessing that didn’t work for some reason, though.”
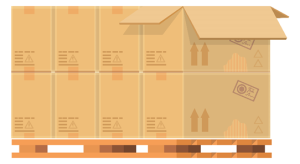
Tabby shook her head again. “No, it didn’t. We ended up with ridiculous situations, where there were urgent jobs on which we could make progress since we had the armatures, and there were bearings available, but we weren’t allowed to use the bearings because they were intended for different jobs. We still had pallets of half-assembled tools clogging the place up.”
“But, of course, you weren’t happy with the bearings just being used for whichever motor was being worked on, either.”
“Darn right, I wasn’t!” Tabby agreed. “Sometimes the bearings got taken for a job which was due later than the one which they’d been ‘stolen’ from, meaning those jobs couldn’t get done on time. That didn’t look good to customers. Trying to avoid it also led to a storeroom full of the wrong bearings which I was talking about earlier. That was actually a fairly big investment in inventory, and you’ve seen how small our assembly area is. That storeroom was taking up a lot of space, you know?”
“Yeah, I understand,” Julian said. “Money tied up in stock, and a big block of non-productive space to hold it all in. I’ll bet the accountants hated it.” He paused for a moment. “Which brings us back to your solution…”
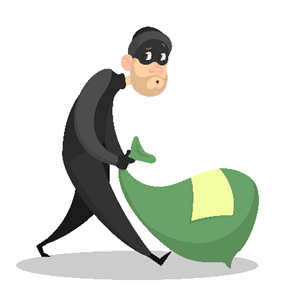
“Right, the common parts schedule. So, the first thing was to find out where bearings intended for the armatures we built, our constraint jobs, were being ‘stolen’ – the non-constraint prebuilt armature jobs were taking parts that were meant for jobs that had to go through the constraint. As long as that ‘stealing’ was going on, then our constraint schedule was just a joke, so we had to get on top of that straight away.”
Julian nodded again and scribbled a note to himself. He was recording this interview on his phone as well, of course, but reading a transcript might not trigger the same thoughts. “And as a result of that, I’m guessing you had to change some policies, too…”
“That’s right,” Tabby said, warming to her theme. “Non-constraint jobs DID NOT use parts intended for constraint jobs. No exceptions, not even if ‘it seemed like a really good idea, and the coffee shop bloke said it was OK’!” she laughed. “Seriously, that was one of the big parts of it – we didn’t care all that much about non-constraint jobs, but we came down like a ton of bricks on stealing bearings intended for jobs that would, or had, gone through armature production. Once we got everyone following that rule, half the battle was won.”
“Uh-huh,” Julian said, “and what was the other half of the battle?”
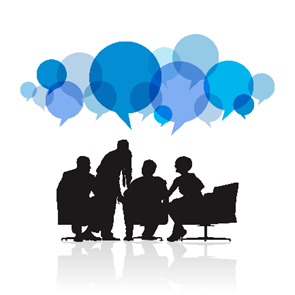
“Ah.” Tabby grimaced, and her happy mood seemed to change for a moment. “Well, that bit wasn’t so easy, actually. If we weren’t allowing non-constraint jobs to ‘steal’ parts, then we had to keep a sort of pool of bearings available, so that we could keep all jobs flowing. Let’s just say that the production of bearings, the mix, and the quantities caused some… enthusiastic discussions amongst the management team.”
Julian looked up at her. “Could you expand on that, please? Some of our readers are going to want to try this themselves, and if there’s anything that might trip them up it would be good for them to know about it.”
Tabby sighed and looked uncomfortable. “Well… OK, but this bit isn’t for publication, OK? Just include it as speculation about how to implement it or something, all right? I don’t want to call anyone out about this.”
“Sure,” Julian agreed, “we do that all the time. Not a problem. So… you had some discussions…?” He let his voice trail off enquiringly.
“Yeah,” Tabby said reluctantly, “we did. There were two main issues, actually. The first one was from the accounting team. The price per unit for the bearings was noticeably lower if we purchased the input materials in big batches, and then produced bearings based on what we had on-hand, and the accounting team couldn’t see why we should willingly pay more for parts we were certainly going to use anyway. Not only was this an issue for bearings but also for all the other inputs we purchased. Dealing with that required digging into the costs of what we were previously doing – storage costs for these huge piles of materials, expediting costs for jobs which were delayed because there were no bearings available, and so on. Eventually, I was able to prove that it would be cheaper to make smaller batches more frequently. Once I managed that, they changed their position quite happily, so credit where it’s due: they were willing to listen to reason.”
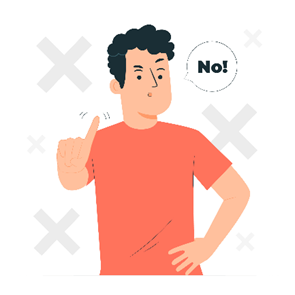
“Right,” Julian said. “But from how you said that, it doesn’t sound like everyone was.”
“No,” Tabitha said. “I don’t really blame him, actually. However, the store manager did not want to reduce the stock levels. He kept on bringing up times when we’d run out of something, and eventually, it got to the point where he didn’t want to be responsible for part availability. Like I said, I don’t actually blame him – if something went wrong it would be him taking the blame, and the less stock we carried the more risk he saw.” She sighed and ran a hand through her hair. “It took a long time to get him to agree to try it.”
“How did you manage that? I mean, if he wasn’t being reasonable about it, then…”
“With four words,” Tabby said, grinning again. “Paranoid-but-not-hysterical. Basically, I agreed with him that it was important to have security of supply and that it was wise to consider edge cases… but that it would be taking caution too far to consider things that only happened once, ten years ago, in a different branch… whatever far-fetched example that was bothering him. I used that exact phrasing, by the way – ‘paranoid but not hysterical.’ I think it actually made a big difference, because it implied that paranoia was reasonable and prudent, but nobody wants to think they’re being hysterical, right?”
“Right,” Julian agreed. “And that was all it took?”
“Not exactly,” Tabby admitted. “I also had to agree that we would reduce stocks gradually and that if we started having problems due to lack of parts we would stop reducing until we could figure out how to prevent that.”
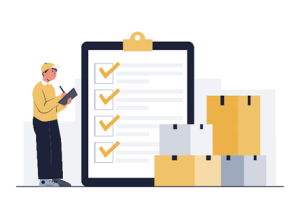
Julian looked back down at his notes. “Right. That leads to something else I wanted to ask about, actually… how do you prevent running out of parts with this ‘common parts schedule’? Because even if you’re being paranoid but not hysterical, you’re still holding much lower stocks than you used to.”
“Ah yes!” Tabby said. “That’s the other big thing that makes this work: a top-up system.”
“Could you explain what you mean by that, please?”
Tabby waved a hand carelessly. “If you like, but you probably already know about it. It’s not all that complicated: you have a small pool of the common parts you need, and whenever you release a job that will use some you also release an order to make a matching number of the common parts the job will use. You track the stock of common parts every day and from time to time halve any obvious excess. Plus, whatever ‘paranoid but not hysterical’ safety margin you’re using.”
“That… actually makes sense,” Julian said slowly. “That’s a good idea!”
“Thank you,” Tabby said. “Now, I’ve got another meeting coming up soon. Was there anything else you wanted to go over?”
“Ah, yes,” Julian said hastily. “Could you quickly go over the benefits OPT has gained from implementing your common parts schedule?”
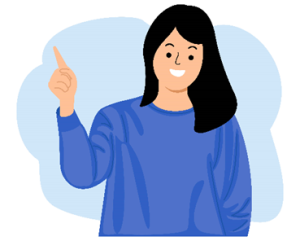
“Sure,” Tabby said and started ticking them off on her fingers. “First thing: significant reduction in the number of jobs finished late because of part stealing. Second: low work-in-progress, so things move faster through the assembly area. Third: we can actually keep our constraint schedule intact, which means our lead times are much more predictable. Fourth: we rarely have to expedite the resupply of common parts. That’s bearings originally, but since it’s been working so well for them, we’re adopting it for other common parts too. Oh, and I suppose there’s also reduced inventory costs, so that’s five.”
“Right,” Julian said and checked his notes again. “I think that’s about everything I had on my list. Any words of wisdom for anyone thinking about trying this themselves?”
“Hmm…” Tabby looked up at the ceiling thoughtfully. “Well, you really need to be running a constraint schedule to get the most out of it, which is a good idea anyway, of course, but if that’s not in place already then you should do that first. And be prepared for debate about the proper level of stock to maintain – you’ll probably have to experiment with that a bit to find the right level, too, so you won’t maximise the benefits straight away.”
“Good advice!” Julian stood up to leave. “Thanks for your time, uh, Tabby. Once the article is ready, we’ll send you a draft for approval. Probably sometime next week, so we can publish it next month.”
“Excellent! All right, come with me, Julian, and I’ll introduce you to Terry. He’s the production manager, and he’ll give you a tour of the plant and let you see the common parts schedule in practice.”
As they made their way to see the production manager, Julian was already planning his article mentally. Tabitha’s ideas had made a big difference at OPT, and it sounded like they would work in lots of other businesses too. It would be interesting to see how other businesses implemented them.