You are in the right place if an increase in output would help, but you need to control costs
- It is often difficult to maintain the rate of completion, as jobs are missing parts, or other prerequisites
- Many times we have to wait for parts, meaning our jobs are not advancing continuously through operations
- Sometimes our scheduled jobs cannot be completed on time due to parts being ‘stolen’ by other jobs
- We often see our work-in-progress rising due to jobs waiting for their reserved parts to arrive
- Too often we find that our supply lead times are longer than our customer-facing lead times
- We suffer too many interrupts due to the expediting of missing parts
- We are holding too much of some types of inventory, tying up excessive amounts of cash
With Finish What Was Started, you will:
- For every job, make visible the prerequisites list (materials, quality standards etc) clearly showing the on-hand status of each prerequisite and when they are expected to clear
- Deploy ‘chase up’ processes to expedite at-risk missing prerequisites.
- Deploy the gap between internal and external lead time to clear as many prerequisites as possible prior to release.
- When a job is released that requires a common part, reserve the common part(s) it needs as soon as they are available
- Implement a replenishment buffer system for common parts
- Implement, test and tune, the ‘in-play’ inventory amounts, with daily top-up ordering, and expediting triggers
With Finish What Was Started, you will ensure that any side effects of the change will be worth it!
While implementing Finish What Was Started, you will address the following common concerns people have. For example:
- Often, we have to rely on past data to order for future demand
- Often, we have to ‘hunt’ for information to understand when a prerequisite is expected to clear
- There are a lot of opinions and ongoing debate about how much stock to hold
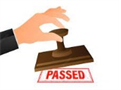
Let’s get started!